Schwedische Wissenschaftler behaupten, dies sei das kleinste 3D-gedruckte Weinglas der Welt – Ars Technica
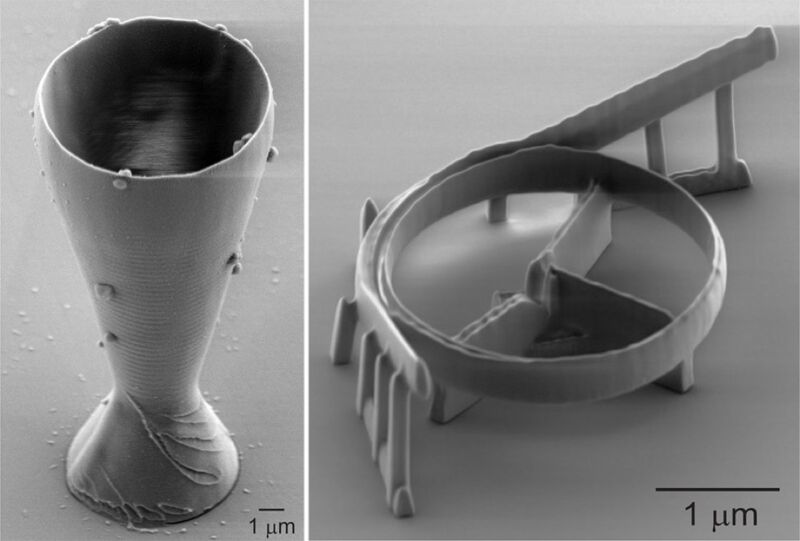
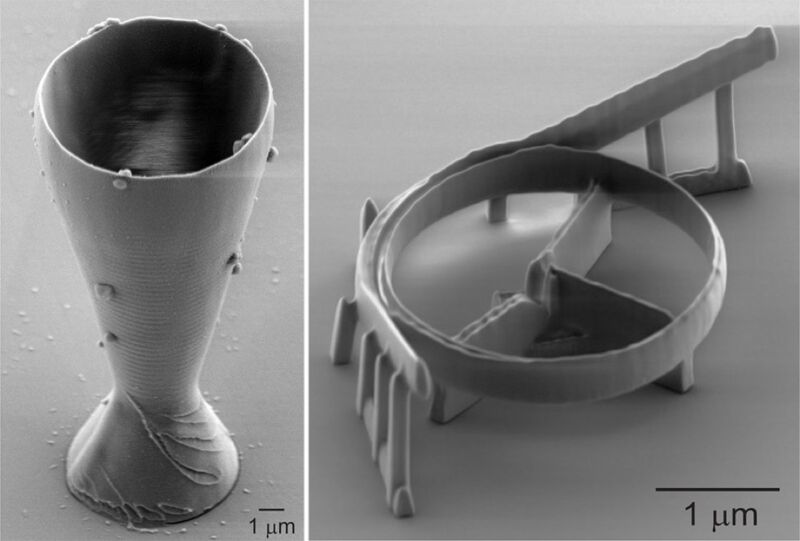
KTH Royal Institute of Technology
Ein Team schwedischer Wissenschaftler hat eine neue Technologie für den 3D-Druck entwickelt Quarzglas Vereinfacht komplexe energieintensive Prozesse. Als Machbarkeitsnachweis druckten sie das kleinste Weinglas der Welt (aus echtem Glas) mit einem Rahmen, der kleiner als die Breite eines Haares war, sowie einen optischen Resonator für faseroptische Kommunikationssysteme – eine von mehreren möglichen Anwendungen dafür 3D-gedruckte Quarzglaskomponenten. Sie beschrieben ihre neue Methode in Das letzte Papier In Naturkommunikation.
„Das Rückgrat des Internets basiert auf Glasfasern, die aus Glas bestehen“, sagte Co-Autorin Christine Gilvason von der KTH Royal Institute of Technology in Stockholm. „In diesen Systemen werden alle Arten von Filtern und Komparatoren benötigt, die jetzt mit unserer Technologie 3D-gedruckt werden können. Das eröffnet viele neue Möglichkeiten.“
Quarzglas (d. h. amorphes Siliziumdioxid) ist laut den Autoren ein Material, das für den 3D-Druck nach wie vor eine Herausforderung darstellt, insbesondere auf mikroskopischer Ebene, obwohl mehrere Ansätze versuchen, diese Herausforderung anzugehen, darunter Lithographie und Einfärbung. Direkte und digitale Lichtverarbeitung . Selbst diese konnten mit einer Ausnahme nur Strukturgrößen in der Größenordnung von mehreren zehn Mikrometern erreichen Studie 2021 das berichtete über eine Genauigkeit im Nanomaßstab.
Aber all das wird genutzt Sol-Gel Prozesse, an denen verschiedene organische Mischungen beteiligt sind, die mit Silica-Nanopartikeln beladen sind. Die endgültigen gedruckten Strukturen sind daher Verbundstoffe, die viele organische Materialien enthalten und daher nicht die wünschenswertesten Eigenschaften von Quarzglas aufweisen (z. B. thermische und chemische Stabilität, Zähigkeit und optische Transparenz über einen weiten Wellenlängenbereich). Es erfordert einen zusätzlichen Sinterschritt bei hohen Temperaturen von etwa 1.200 °C (2.192 °F) über mehrere Stunden, um die organischen Rückstände zu entfernen und diese Eigenschaften zu erreichen. Dieser besonders energieintensive Schritt schränkt die Einsatzmöglichkeiten erheblich ein, da nur Substratmaterialien verwendet werden können, die höheren Temperaturen standhalten. Einige Ansätze erfordern auch den Zusammenbau 3D-gedruckter Strukturen in eine endgültige Form, was im Mikrometermaßstab eine Herausforderung darstellt.
Bei der Entwicklung ihrer alternativen 3D-Drucktechnologie für Quarzglas hat Gylfason et al. Einbiegen in Wasserstoffsilsesquioxan (HSQ), ein anorganisches, silikaähnliches Material, das durch Elektronenstrahlen, Ionenstrahlen und bestimmte Wellenlängen von ultraviolettem Licht geformt werden kann. Ein großer Vorteil besteht darin, dass ihre Methode nicht auf organische Verbindungen als Photosensibilisatoren oder Bindemittel angewiesen ist, die auf dem Substrat verbleiben, wie es bei der Lithographie oder dem direkten Tintenschreiben der Fall ist. Stattdessen beruht ihre Methode auf der direkten Vernetzung anorganischer HSQs.
Der Prozess besteht aus drei Hauptschritten. Zuerst tropften sie in organischen Lösungsmitteln gelöstes HSQ auf ein Substrat. Sobald der HSQ trocknet, zeichnen sie die gewünschte 3D-Form mit einem fokussierten Laserstrahl im Subpikosekundenbereich nach. Abschließend wird das nicht abgedeckte HSQ mit einer einfachen Kaliumhydroxidlösung aufgelöst. Die Raman-Spektroskopie der gedruckten Mikrostrukturen zeigte alle erwarteten Eigenschaften von Quarzglas.
Es gab jedoch auch Restspuren von Wasserstoff und Kohlenstoff. Für Anwendungen, die reineres Quarzglas erfordern, können restliche organische Stoffe durch Glühen der Strukturen bei 900 °C (1.652 °F) entfernt werden – ein zusätzlicher Schritt, der jedoch bei einer viel niedrigeren Temperatur als der übliche zusätzliche Sinterschritt erfolgt. Anschließend wurde das Spektrum der Strukturen an ein handelsübliches Quarzglassubstrat angepasst. Während das Glühen der 3D-Mikrostrukturen dazu führen kann, dass sie schrumpfen oder sich verformen, stellten die Autoren fest, dass die maximale Schrumpfung ihrer Quarzglasstrukturen etwa 6 Prozent betrug, verglichen mit 16 bis 56 Prozent für Glasobjekte, die mit Lithographie- und Direkteinfärbemethoden hergestellt wurden . . .
Zusätzlich zu einem kleinen Proof-of-Concept-Weinglas und einem optischen Resonator prägten die Autoren eine kleine Version des KTH-Logos, einen Ausleger und eine konische Spirale sowie eine Glasfaserspitze aus Quarzglas ein. Sie glauben, dass ihre Methode auch zur Herstellung maßgeschneiderter Linsen für medizinische Geräte und Mikroroboter genutzt werden könnte. Die Beschichtung von 3D-gedruckten Mikrostrukturen mit Diamant-Nanopartikeln oder Eisen-Nanopartikeln könnte eine weitere Ausarbeitung der Integrationseigenschaften der hybriden Quantenphotonik ermöglichen bzw. die magnetische Kontrolle über die Bewegung der Strukturen aufheben.
„Die Bedenken bei der Integration von 3D-Druckverfahren sind in der Regel für verschiedene Anwendungen unterschiedlich.“ sagte Co-Autor Bo Han Huang, ein Doktorand an der KTH. „Obwohl eine Optimierung unserer Methode für verschiedene Anwendungen noch erforderlich ist, glauben wir, dass unsere Methode einen wichtigen und notwendigen Durchbruch für den 3D-Druck auf Glas für den Einsatz in praktischen Szenarien darstellt.“
DOI: Nature Communications, 2023. 10.1038 / s41467-023-38996-3 (über DOIs).
„Musikfan. Sehr bescheidener Entdecker. Analytiker. Reisefreak. Extremer Fernsehlehrer. Gamer.“