Dow und Mura bauen fortschrittliche Recyclinganlage in Deutschland
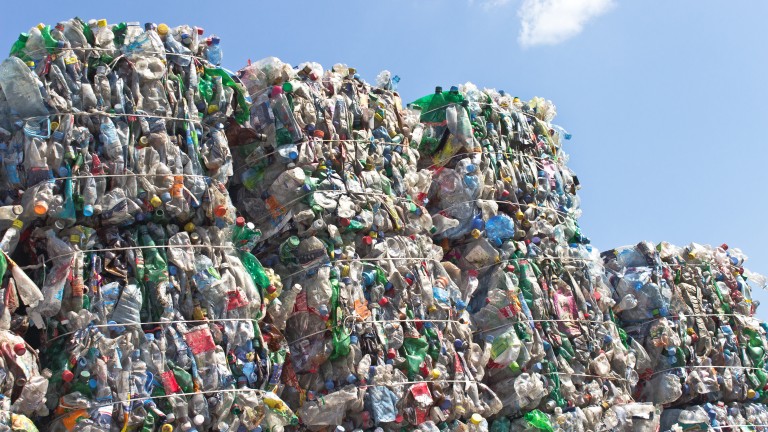
Dow Und Mura-Technologie haben die nächste Phase ihrer laufenden Zusammenarbeit veröffentlicht. Mura plant den Bau einer neuen Anlage am Standort Pollen von Dow in Deutschland – die jüngste in einer Reihe von Anlagen, die in den USA und Europa geplant sind – und wird voraussichtlich die erste am Standort von Dow sein. Das Projekt strebt eine endgültige Investitionsentscheidung bis Ende 2023 an.
Die neue Anlage von Mura in Böhlen in Deutschland, die voraussichtlich 2025 in Betrieb gehen wird, wird eine erweiterte Recyclingkapazität (KTA) von etwa 120 Kilotonnen pro Jahr bei voller Durchflussrate bieten. Diese und andere geplante Einheiten werden bis 2030 in Europa und den USA zusammen 600 KTA an fortschrittlicher Recyclingkapazität hinzufügen.
„Die Fortsetzung und das Wachstum der Zusammenarbeit von Dow und Mura ist ein weiteres Beispiel dafür, wie strategisch Dow beim Schutz von zirkulären Rohstoffen und der Unterstützung fortschrittlicher Recyclingtechnologien vorgeht“, sagte Issam Shomali, Dow Business Vice President für Rohstoffe und Rohstoffe.
„Wir steigern weiterhin die Fähigkeit von Dow, recycelte Inhaltsstoffe als Rohstoffe zu verwenden, und investieren weiterhin in die beste verfügbare Technologie, um unser zirkuläres Geschäftsmodell für Kunststoffe voranzutreiben“, sagt Diego Donoso, Präsident von Dow Packaging & Specialty Plastics. „Die Diversifizierung unseres Ausgangsmaterials Schiefer und die Dekarbonisierung unserer Vermögenswerte werden uns dabei helfen, das Ziel von Dow einer nachhaltigen, kohlenstoffarmen Zukunft zu erreichen und die starke und wachsende Kundennachfrage nach zirkulären Polymeren zu befriedigen. Dies wird ein bedeutender Schritt zur Verringerung unserer Abhängigkeit von Neuware sein Rohstoffe auf fossiler Basis.“
Die geplante Anlage baut auf der bestehenden Zusammenarbeit von Dow mit Mura auf, wobei zunächst geplant ist, eine Anlage in Teesside, Großbritannien, unter Verwendung des HydroPRS-Verfahrens von Mura zu bauen, die voraussichtlich 2023 mit einer anfänglichen 20-KTA-Produktionslinie in Betrieb gehen wird. Der Standort Böhlen, Deutschland, wird voraussichtlich zusammen mit den Produktionsanlagen von Dow angesiedelt, was eine große Kapazität für Kunststoffabfälle ermöglicht und die Versorgung der Industrie mit Vollkreislauf-Rohstoffen erheblich erhöht. Dieses zirkuläre Ausgangsmaterial wird aus Kunststoffabfällen gewonnen, die derzeit zur Verbrennung oder Deponierung bestimmt sind, wodurch die Abhängigkeit von neuen fossilen Ausgangsmaterialien verringert wird und Dow in die Lage versetzt wird, recycelte Kunststoffe herzustellen, die von globalen Marken stark nachgefragt werden, insbesondere für sensible High-End-Märkte wie Lebensmittel. und medizinische Anwendungen.
Dow beabsichtigt, die Vorteile von Kollokationen zu nutzen, die die Kosten für die Skalierung fortschrittlicher Recyclinganlagen erheblich senken können. Darüber hinaus wird erwartet, dass die Kollokation der Einrichtungen von Mura an Dow-Standorten die CO2-Emissionen reduzieren wird, indem der Transport von Abgasen reduziert wird und der Gasausstoß aus dem fortschrittlichen Recyclingprozess wieder in Kunststoff umgewandelt werden kann, wodurch sichergestellt wird, dass Nebenprodukte nicht verschwinden . Abfall
Das fortschrittliche Recyclingverfahren HydroBRS (Hydrothermal Plastic Recycling Solution) von Mura verwendet überkritischen Dampf, um die meisten Kunststoffarten – einschließlich flexibler und mehrschichtiger Kunststoffe, die zuvor als nicht recycelbar galten – in die ursprünglichen Öle und Chemikalien umzuwandeln, aus denen sie hergestellt wurden. Diese können verwendet werden, um neue, neue Kunststoffe herzustellen, die sogar für Verpackungen mit Lebensmittelkontakt geeignet sind.
Das Verfahren von Mura ermöglicht es, dasselbe Material immer wieder zu recyceln, was bedeutet, dass es das Potenzial hat, Einwegkunststoffe zu eliminieren und zu verhindern, dass sie auf Mülldeponien landen oder verbrannt werden. Dies hat zusätzliche Kohlenstoffvorteile, da fortschrittliche Recyclingprozesse im Vergleich zur Verbrennung voraussichtlich etwa 1,5 Tonnen Kohlendioxid pro Tonne recyceltem Kunststoff einsparen werden.
„Unheilbare Internetsucht. Preisgekrönter Bierexperte. Reiseexperte. Allgemeiner Analyst.“